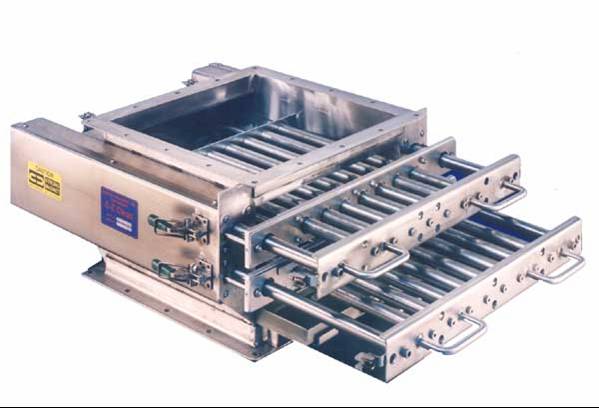
Proper magnet selection is imperative in ensuring quality products and protecting processing equipment. Metal contamination can occur throughout any stage of the manufacturing process.
Suppliers can deliver raw product with metal contamination, process machinery can lose nuts and bolts or generate fines from abrasive products, and human error can introduce tools or other items to the process.
By properly placing magnetic separators at strategic locations, you can greatly reduce the risk and liability of metal contamination in your final product.
Magnetic separation equipment should be placed where incoming ingredients are being introduced to the process. This would include truck and rail car unloading, bulk bag unloading, and any other product receiving or area where ingredients are added to the process.
Within the process system magnetic separators should be placed prior to equipment that is easily damaged by ferrous contaminants to reduce costly downtime for repairs.
Placement after equipment that has a known margin for failure will ultimately help to produce a quality end product. Finally, packaging/loadout areas should have magnetic protection to ensure metal free quality products.
Style Considerations
To determine which style of magnetic separator is correct for your application, several things must be considered.
Answering the following questions will provide enough information for Puritan Magnetics, Inc. to properly advise you as to which magnet and size to choose.
1. What is the product?
2. What is the bulk density?
3. What is the flow rate?
4. Is it powder, granular, lumpy, dry, moist, etc.?
5. How is the product conveyed? Gravity? Pneumatically? Mechanically?
6. If by gravity, is it vertically or on an angle and what is the spout size?
7. If pneumatically, is it a dense or dilute phase system and what is the line size?
8. If mechanically, is it by belt conveyor, screw conveyor, etc.?
9. What size is the ferrous contaminants you are trying to extract, large, medium or fines?
Cleaning
Once a magnet has extracted the metal contaminant from the product, the magnet itself has to be periodically cleaned. Most magnetic separators are available with options to simplify cleaning.
This is especially helpful with rare earth magnetic separators due to their powerful nature and difficulty in cleaning.
Manual cleaned magnets require an operator to access the magnet’s working surface and pull or wipe off any metal contaminants. This can prove to be difficult and dangerous. Sharp metal pieces could easily injure someone.
EZ CLEAN magnets incorporate a device that still requires operator interaction but does so in a way that metal is released without having to come in contact with it.
POW-R CLEAN magnets are magnets that are continuously self cleaning themselves or operate at the push of a button or automatically if linked to an automated system. These are especially convenient when accessibility to the magnet is difficult or the magnet is very large and cumbersome making cleaning difficult.
Complete our Magnet Application Form for a prompt quotation!
What Magnetic Separator do you need?
Magnetic Separators for dry free-flowing products when bridging is NOT a concern:
Magnetic Separators for dry free-flowing products when bridging is a concern:
Magnetic Separators for continuous cleaning operations:
Magnetic Separators for Liquids:
Magnetic Separators for Pneumatic Conveying: